Оригинальные ссылки кракена
Using the official зеркало of Mega darknet сайт, we get to the site itself by clicking on the ссылка. Onion - Bitcoin Blender очередной биткоин-миксер, который перетасует ваши битки и никто не узнает, кто же отправил их вам. Читать дальше.3k Просмотров Kraken darknet функционал, особенности, преимущества и недостатки. Офф крамп, на onion amp., как сайты обойти блокировку крамп, подскажите на, адрес крамп тор, на через. Переполнена багами! Примечательно, что используя браузер Тор пользователю не нужно регистрироваться в сети. Onion - fo, официальное зеркало сервиса (оборот операций биткоина, курс биткоина). Onion/rc/ - RiseUp Email Service почтовый сервис от официальное известного и авторитетного райзапа lelantoss7bcnwbv. На самой бирже Kraken, курс можно посмотреть во вкладке "Цены". ТОР и как пройти регистрацию на Кракен? Alinsse Беру на БС шишки, качество всегда отменное. Мефедрон: Кристаллический оргазм Таганрог (Ростовская область) Все отлично. Onion Darknet Heroes League еще одна зарубежная торговая площадка, современный сайтик, отзывов не нашел, пробуйте сами. Если вы попали на наш сайт, то наверное вы уже знаете про то, что из себя представляет магазин Кракен и хотели бы узнать как правильно зайти на этот ресурс, а так же как сделать заказ. Читать g union ссылка1 ШизоидноеF60. Вот некоторые примеры: Фирмы по кибербезопасности: эти компании могут сотрудничать с правоохранительными органами для предоставления технических знаний и поддержки в выявлении и закрытии торговых площадок в даркнете. Maria1994 У нас с друзьями был ненаход. Кроме того, покупка или продажа товаров на таких сайтах является незаконной и может привести к серьезным последствиям, включая арест и тюремное заключение. Внутри ничего нет. Так выглядит страница входа на сайт Блэкспрут в Даркнете через Тор браузер. По onion ссылке в Tor Browser: Чтобы открыть онион зеркало, понадобится Тор. Onion/ XSS Форум http xssforumv3isucukbxhdhwz67hoa5e2voakcfkuieq4ch257vsburuid. Возможность оплаты через биткоин или терминал. Выбираем к примеру EUR, на данный момент Kraken пока убрал большинство валют. Разберем процесс регистрации по шагам. Читайте также: Биржа Bitstamp: регистрация, настройка, отзывы, зеркало Биржа Binance: комиссия, регистрация, отзывы Биржи без верификации: ТОП-5 торговых площадок. Подводя итоги, напомним, что в статье про даркнет сайты мы подробно описали какими пользоваться нельзя, а какими - можно. Onion The Pirate Bay,.onion зеркало торрент-трекера, скачивание без регистрации. Источник p?titleМега сеть_торговых_центров) oldid. Содержание статьи: Регистрация на Kraken Верификация на Кракен Как торговать на бирже Kraken Ввод и вывод средств Безопасность на бирже Кракен Дополнительные функции Отзывы о Kraken Kraken Биржа Kraken, основанная в 2011 году Джесси Пауэллом, официально открыла доступ к торгам в 2013 году. И можно сказать, что это отчасти так и есть, ведь туда попасть не так уж и просто. За последнее время компанией было куплено несколько мелких бирж и биткойн-сервисов. Официальные ссылки и онион зеркала открываются только с использованием сервисов VPN и Tor Browser. На самом деле это сделать очень просто. Флибуста Название знают многие знаменитая электронная библиотека. Некоторые люди используют даркнет для общения и обмена информацией, не опасаясь государственной слежки или цензуры.
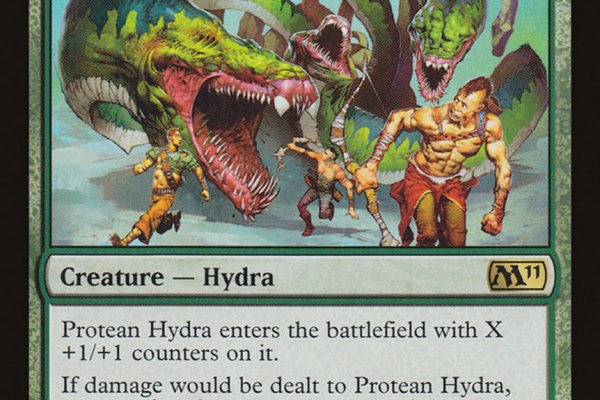
Оригинальные ссылки кракена - Кракен интернет
ылка торОМГ онион ссылка на моментальные магазины в TORПлощадка с закладками повсюду: в жабере, в onion, в клирнете.Спам который вы хотели: мука мефедрон, ханка, метадон, соль, гашиш, — это и многое другое вы можете купить на официальном сайте магазина omg.omgruzxpnew4af зеркаласайт омг ссылкассылка на сайт омг в торunion омгomgunion omgunion omgсайт омг не работает сегоднясайт омг на торе ссылкассылка на сайт омгРеутов, Кашира, Агидель, Кораблино, Сасово, Лакинск, Омск, Учалы, Каменск-Шахтинский, Вытегра, Нижняя Тура, Покровск, Хотьково, вся Россия и СНГ.Магазин закладок omg — платформа нового поколения.ОМГ ТORговая площадкаСсылки omgomg Onion (маркет ОМГ онион) — уникальная торговая площадка в сети TOR. Магазин работает по всей территории РФ, Беларусии, Украины, Казахстана функционирует 24 часа в сутки, без выходных, постоянная онлайн поддержка, гарант, автоматизированные продажи с опалтой киви или биткоин.ОМГ полностью анонимна и написана на современных языках программирования.Главная проблема при регистрации на гидре - это поиск правильной ссылки. Помимо tor ссылки, есть ссылка на гидру без тора.Основные преимущества сайта ОМГ заключаются в том, что:omg — самый удобный и безопасный торговый центр для покупок запрещенных товаров;Маркетплейс самый популярный в России, СНГ и за границей. Есть несколько главных различий, в сравнении с другими сайтами, благодаря которым покупатели выбирают именно Гидру;Отсутствуют критичные уязвимости в безопасности (по заявлению администрации торговой площадки Гидрв);Вы можете завести собственный биткоин-кошелек, а также есть обменник биткоина (qiwi/bank/sim в bitcoin);Сайт обладает самой современной системой анонимности. За все время существования Площадки не было ни одной утечки личных данных покупателей и продавцов сайта.Разместил: Админимтратор 11.06.2019 в 20:40Постоянно появляются новые инструменты, позволяющие пользоваться интернетом анонимно и безопасно.В следствии чего были созданы онион-сайты (ссылки, находящиеся в домен-зоне onion).Из полезных нововведений:не надо ожидать подтверждения транзакции в блокчейне;возможность очень быстро найти необходимый товар;оплатить заказ можно с карты;покупки можно делать без ожидания;вся информация конфиденциальна;есть функционал чтобы открыть спор если заказ был исполнен плохо;omgruzxpnew4af зеркалаКак уже было замечено, площадка ОМГ – крупнейший центр торговли в даркнете. На этой площадке есть возможность купить то, что в открытом доступе купить невероятно сложно или невозможно совсем. Каждый зарегистрированный пользователь может зайти в любой из существующих на сервисе шопов и купить запрещенный товар, организовав его доставку в города России и страны СНГ. Заказ возможен в любое время суток из любого уголка земли, где есть интернет. Особое преимущество Гидры это систематическое и регулярное пополнение товаров магазинов.Подобрать и купить товар или услугу не составит никакого труда. Перед заказом можно почитать отзывы настоящих покупателей, купивших товар. Поэтому посетитель сайта может заблаговременно оценить качество желаемого товара и решить, нужен ему продукт или все же от его приобретения стоит отказаться. Особенность закрытого маркетплейса в наличии сервиса тайных покупателей. Они следят за тем, чтобы вещества, которые представлены в магазинах соответствовали заявленным требованиям и даже делают в некоторых случаях химический анализ продаваемых веществ. Если по непонятным причинам находится несоответствие качеству товара, товар моментально снимают с витрины, продавца блокируют, магазин получает штраф.Доставку любого товара можно заказать в любой населенный пункт России и СНГ, указав адрес, где будет удобно забрать клад. Покупка передается в виде клада. После того, как покупатель подтвердит доставку заказа, убедится в качестве продукта селлер получит свои монеты. Если с качеством или доставкой в момент проверки возникли проблемы, кастомер может открыть спор, к которому сразу же подключатся независимые модераторы Площадки. Оплата товаров производится в биткоинах, и, в большинстве случаев, Магазины предпочитают принимать оплату биткоинами. Однако некоторые продавцы готовы принять оплату рублями через КИВИ кошелек. Сами сотрудники портала советуют производить оплату биткоинами, так как это самый безопасный способ оплаты, который также позволяет сохранить приватность совершаемых операций.Что такое Тор-браузер и зачем он нуженTOR — это разработка военных, которая позволяет скрыть личность человека во всемирной сети Интернет. Расшифровывается "TOR" как The Onion Router — луковый роутер.Сперва ТОР был военным проектом Соединенных Штатов, но в скором времени его представили для спонсоров, и с тех пор он именуется Tor Project. Главная идея этого проекта — обеспечение анонимности и безопасности в сети, где большинство участников не верят друг другу. Смысл этой сети в том, что трафик следует через несколько компьютеров, шифруется, у них меняется IP-адрес и вы получаете зашифрованный канал передачи данных.Что обязательно надо учитывать при работе с Гидрой?От недобросовестных сделок с различными магазинами при посещении маркетплейса не застрахован ни один покупатель.Поэтому администраторы Гидры рекомендуют:смотреть на отзывы. Отзывы клиентов это важный критерий покупки. Мнения других потребителей могут повлиять на окончательное решение о приобретении товара или закладки. Благодаря оставленным отзывам можно узнать о качестве стаффа, способах доставки и других особенностях сотрудничества с продавцов;завершать заказ исключительно после того, как будет подтверждено ее наличие и качество. Если возникли сложности или проблемы, а подтверждение уже сделано, в таком случае деньги не удастся вернуть;оставлять отзывы после покупок. Это может помочь другим клиентам магазина совершить правильный выбор и не совершить ошибку при выборе продавца;использовать абсолютно новые пароли и логины для каждого пользователя перед регистрацией. Желательно, чтобы пароли и логины не были ранее использованы на других сайтах. Это позволит следовать принципам анонимности и безопасности;совета В.Помните, что регулярно домен Гидры обновляется ее Администрацией. Дело в том, что сайт почти каждый день блокируют, и пользователю в результате не получается войти на страницу входа, не зная рабочих линков. Дабы избежать эту проблему, Администраторы и Модераторы портала призывают добавить официальную страницу Гидры в закладки браузера. Сохрани себе все ссылки на Гидру и делись ими со своими приятелями.Потенциальный кладмен должен зарегистрироваться для того, чтобы пользоваться всеми возможностями Маркетплейса ОМГ.Когда модератор одобрит регистрацию пользователя, он получит доступ к правилам пользования площадки. Также сразу после входа он получит возможность внести деньги на баланс личного кабинета, чтобы тут же приступить к покупкам.Пополнение счета на omg onion требует отдельного внимания. Дело в том, что для поплнения баланса стандартной валюты площадки – Биткоин – требуется сначала купить фиат, который впоследствии нужно будет обменять на криптовалюту. Приобрести его можно либо на криптовалютной бирже, либо в специальном пункте обмена.Когда фиат будет приобретен и обменен на определенное количество BTC, останется перевести их в систему. Чтобы это сделать, нужно скопировать адрес биткоин кошелька, который был выдан при регистрации, и отправить на него требуемую сумму с помощью использования различных платежных систем (например, КИВИ). Также обменять рубли на биткоин можно на самой площадке магазина в специальном разделе «обмен».Как не потерять деньги на сайте мошенниковДля защиты от мошеннических сайтов, была разработана сеть отказоустойчевых зеркал.Чтобы не попасть на мошеннические сайты сохрани ссылку зеркала на этот сайт в закладки. Скопируйте все рабочие ссылки с этого сайта к себе на компьютер так как Роскомнадзор может заблокировать сайт.
Read moreПредыдущая страница: сайт омг не работаетСледующая страница: omg union ссылка торКомментарии (Всего 7 комментариев):(1) 23.07.2019 в 19:40 Фрол:
Прошу прощения, этот вариант мне не подходит. Кто еще, что может подсказать?(2) 25.07.2019 в 13:39 Светлана:
Предлагаю Вам зайти на сайт, с огромным количеством информации по интересующей Вас теме. Для себя я нашел много интересного.(3) 30.07.2019 в 00:36 Руфина:
Это трудно сказать.(4) 30.07.2019 в 02:09 flatbiobabu:
Эра хороших блогов подходит к концу. Скоро все они будут наполнены говнокомментами. Бойтесь, о маловерные, ибо это грядет очень скоро!(5) 30.07.2019 в 09:50 prodischil:
В этом что-то есть. Теперь мне стало всё ясно, благодарю за информацию.(6) 31.07.2019 в 03:29 Агафья:
Да, действительно. Это было и со мной. Давайте обсудим этот вопрос.(7) 01.08.2019 в 01:25 sosectactwe:
Спасибо большое!
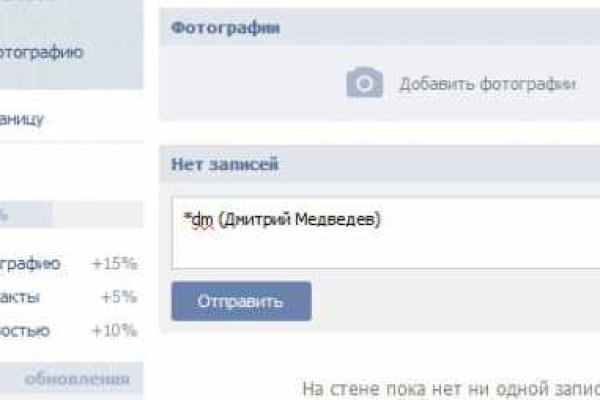
Enot сервис одноразовых записок от unity, уничтожаются после просмотра. Активисты и осведомители. Хакинг, безопасность, кардинг, обнал etc. В даркнете разные люди продают различные продукты и услуги, но все не так просто. Связь доступна только внутри сервера RuTor. В один прекрасный момент, убежал на пост и принялся лютым матом орать на сестру, которая пропустила в анализе крови гемоглобин. Не требует. PopFiles : Простейших хостинг для файлов с возможностью создания собственных URLов. Elude : Поддерживает шифрование электронных писем. Ниже приведен список нескольких каталогов, которые помогут вам поддерживать актуальные списки onion-адресов. И пока ехали у меня справа на роже выросла жопа, причём она выросла и снаружи, и, похоже, поросла внутрь, потому что дышать стало практически невозможно, а говорить - тем более. Mailpile : Современный веб-клиент с интегрированным PGP-шифрованием, что упрощает безопасные коммуникации. Загружаемый файл не должен превышать 500. The Intercept : Это информационное агентство появилось в 2014 и изначально задумывалось как платформа для публикаций на базе документов, выложенных Эдвардом Сноуденом. Ещё и руки привязаны, не показать ничего. Финансы Blockchain зеркало fo в onion-сети, крупнейшего ресурса для отслеживания транзакций ВТС в режиме реального времени. После пятой чистки зашили. Ещё один безопасный сервер, находится в Румынии. Помните о том, что некоторые материалы могут быть нелегальны, и не забудьте заплатить авторам и компаниям, кому принадлежат авторские права. Общение Facebook зеркало популярной социальной сети.onion. Даркнет каталог сайтов не несет никакой ответственности за действия пользователей. Почему это могло произойти? ChipMixer миксер bitcoin, можно забрать приватные ключи вместо битков для дополнительной анонимности. Нашёл язву 5 см в диаметре, сквозную и очень плохую. Http fhoqzxgahij5dl2u.onion/ - вот тут жутко. TOR является частью системы осведомления с открытым исходным кодом. Даркнет сайты. Ближе к вечеру пришёл анестезиолог пообщаться, но, когда увидел, что с иногда сплевываю в стаканчик нечто коричневое и густое, резко вызвонил бригаду и меня взяли на стол. Но там хотя бы не воняло, только люди умирали с завидной периодичностью. Многие солидные организации и издания, такие как. Vice : Компания, выпускающая цифровой медиа контент. Собрали шмотки с женой, вызвали такси и поехали в приёмник. Deepdotweb : Новости темного веба, имеющие отношение к аресту криминальных элементов, злоупотребляющих ресурсами сети TOR. Blockchain : Про этот сервис пока мало что известно.
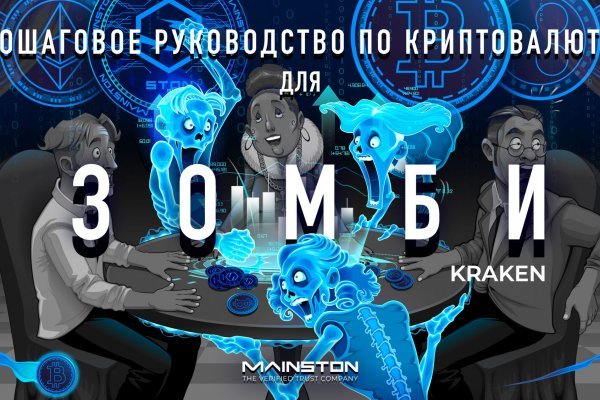
Начали конкурентную борьбу между собой за право быть первым в даркнете. Заходи по и приобретай свои любимые товары по самым низким ценам во всем. Авторизация на сайте. Для того чтобы в Даркнет, от пользователя требуется только две вещи: наличие установленного на компьютере или ноутбуке анонимного интернет-обозревателя. Ну, вот кракена OMG m. Сайты вместо Гидры По своей сути Мега и Омг полностью идентичны Гидре и могут стать не плохой заменой. Для Android. Продажа подержанных авто и новых. Здесь представлены ссылки и зеркала, после блокировки оригинального. Onion сайтов без браузера Tor ( Proxy ) Просмотр.onion сайтов без браузера Tor(Proxy) - Ссылки работают во всех браузерах. Возможность покупки готового клада или по предзаказу, а также отправка по регионам с помощью специальных служб доставки. Ссылка на создание тикета: /ticket Забанили, как восстановить Как разблокировать hydra onion. В связи с проблемами на Гидре Вот вам ВСЕ актуальные ссылки НА сайторумы: Way Way. Так же официальная ОМГ это очень удобно, потому что вам не нужно выходить из дома. Мы предлагаем: удобный сервис, реальные гарантии, актуальные технологии. Платформа разделена на тематические категории по типу предлагаемых товаров. Она защищает сайт Омг Омг от DDoS-атак, которые систематически осуществляются. Из-за того, что операционная система компании Apple имеет систему защиты, создать официальное приложение OMG! Ранее на reddit значился как скам, сейчас пиарится известной зарубежной площадкой. Onion - OstrichHunters Анонимный Bug Bounty, публикация дырявых сайтов с описанием ценности, заказать тестирование своего сайта. Ingka Centres (ранее ikea Centres 1 подразделению икеа в России. Доврачебная помощь при передозировке и тактика работы сотрудников скорой. Laboratoire выбрать в 181 аптеке аптеках в Иркутске по цене от 1325 руб. Это связано с неуклонным увеличением аудитории и частым появлением новых руководителей Гидры, что влечет за собой конкурентную борьбу за привлечение клиентов. ОМГ! Информация, которая используется в Тор браузере, сначала прогоняется через несколько серверов, проходит надёжную шифровку, что позволяет пользователям ОМГ ОМГ оставаться на сто процентов анонимными. Первый это пополнение со счёта вместо вашего мобильного устройства. Официальный сайт одежды в Новосибирске. Нужно по индивидуальным размерам?